Laurence Quinn, architect and founder of Modern Works, on the power of production
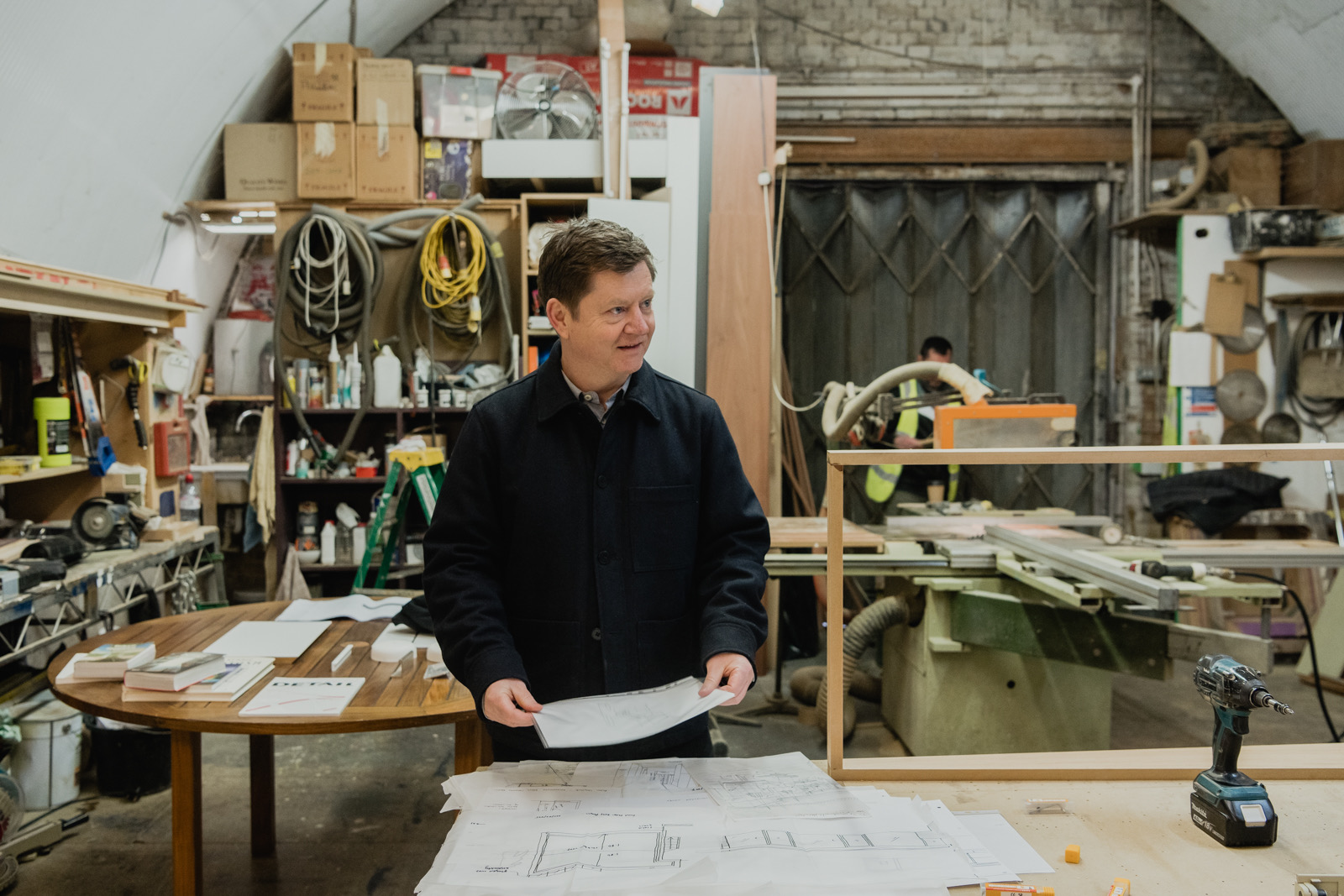
Laurence Quinn studied architecture at the Royal College of Art in London before relocating to Milan for seven years. There he worked with the internationally renowned designer and architect Antonio Citterio in Brianza – an area synonymous with excellence in design and manufacturing. “Gio Ponti, Franco Albini, Carlo Scarpa – everything they designed came out of Brianza,” says Laurence. When he returned to the UK in 2012, he set up his own practice, Quinn Architects. But he remained fascinated with the manufacturing process: “Production has always been at the centre of the work we do,” he reveals.
As the practice expanded, Laurence found it difficult to achieve the quality and finish he demanded from the contractors working on their smaller projects. Seven years ago, a tricky project on the roof of the Barbican paved the way for a new venture. Laurence rented a workshop in Camberwell, south-east London, and launched Modern Works – what he describes as “a 3D sketchbook” for his architecture firm. “Our aim is to apply our architectural care and attention to the activity of making,” says Laurence. In doing so, Modern Works has emerged as the solution for clients seeking a sensitive, uncompromising update on buildings and interiors of architectural interest.
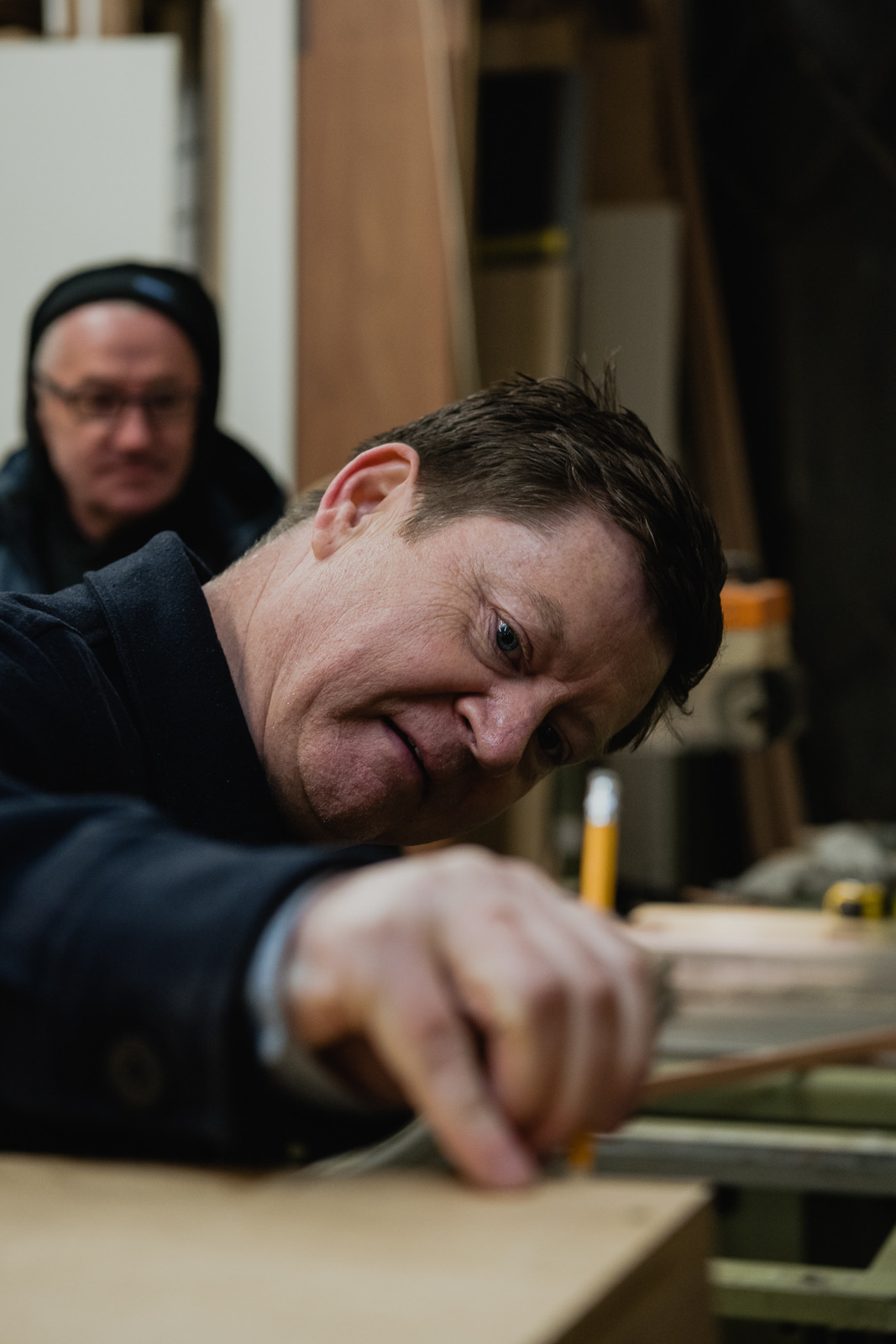
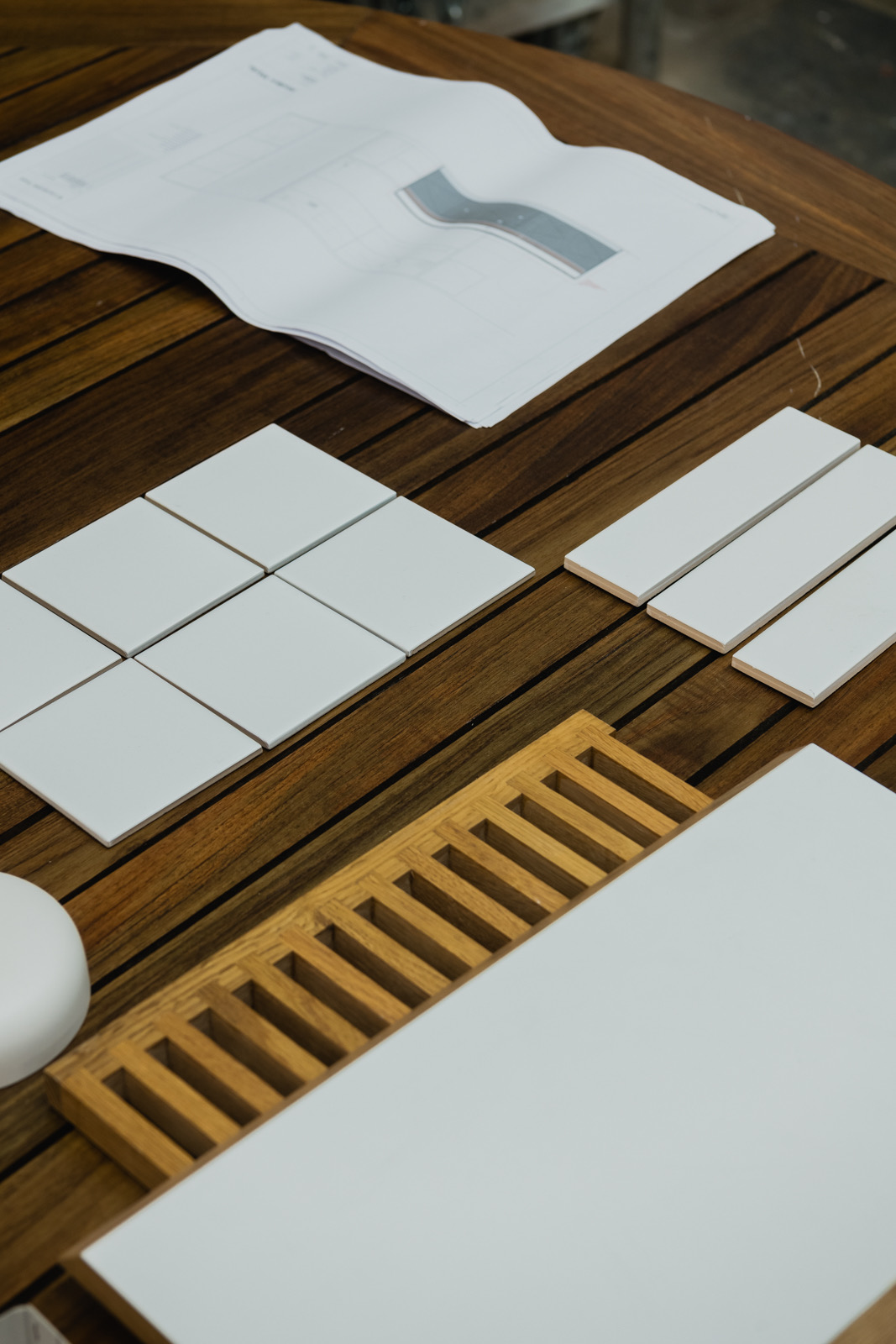
Laurence: “The idea for Modern Works came about while I was working on a new proposal for an existing client who lived in a penthouse at the top of the Barbican’s Cromwell Tower. We had received rare planning consent to build a new timber structure on the roof – 40 floors up.
“There was a latent defect in the building, so we gathered all parties together and agreed that the best way to solve the problem was in fact to enclose the roof. We were given consent to create a beautiful glazed box on top of the building. The trouble was, no one would build it. It was too complicated, too small, too difficult, so we decided to take on the project ourselves…
“We knew that if we approached the construction process with the same rigour as the design process, a lot of seemingly insurmountable problems could be fixed. So we did our research and we learnt that the goods lift in the Barbican was actually used to build the flats. We found out that – in special circumstances – it can drop down a floor, so that you can load up the roof with materials and bring them easily up to the top floor.
“That lift became a metaphor for how we approach projects. It launched our curiosity and made us realise that, quite often, contractors working on a smaller scale don’t have the resources to make things the way we want them to be made. We realised we had a network of talented makers we enjoyed working with and that we could assemble a team to deliver these projects ourselves, so we decided to take the plunge.
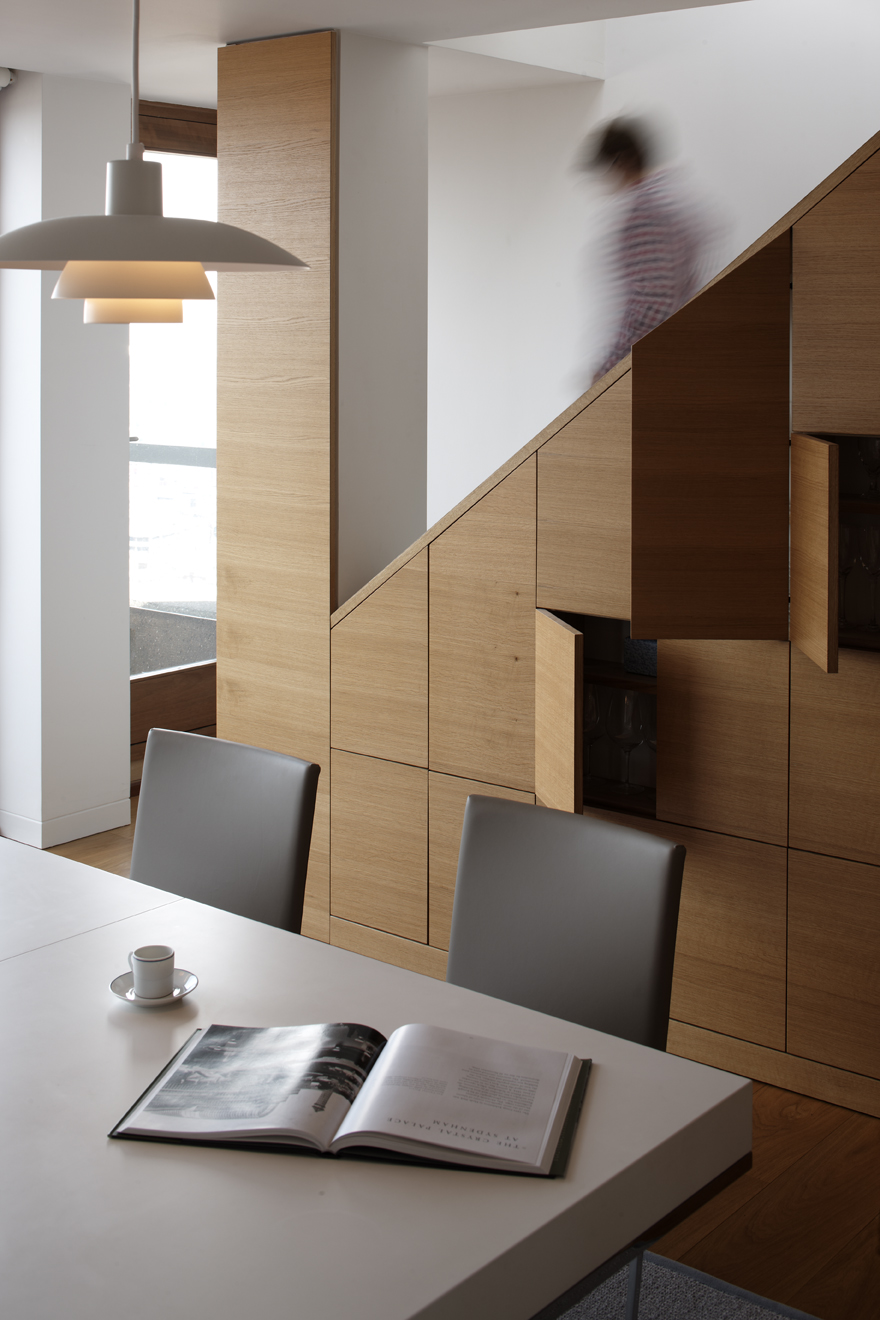
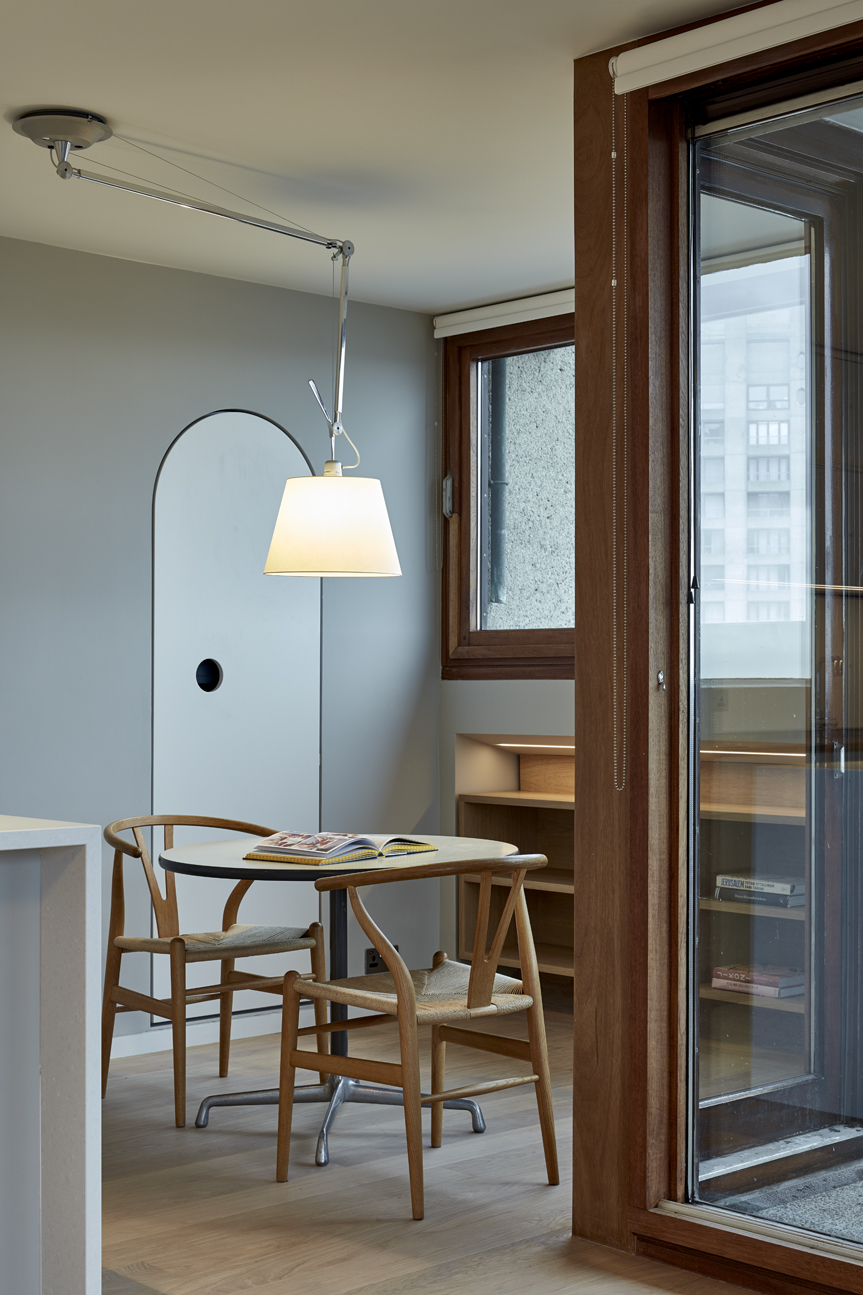
“Forming Modern Works has allowed us to take control of the whole process from the initial design through to construction and completion. This way, we are able to guarantee our designs are built to last, using the best materials available, at the right cost. Our clients come to us for the level of quality and finish we provide, as well as our design-led approach and ability to make quick, well-informed decisions that work within their budget.
“The Barbican was a great place for us to start because it represents the kind of projects we’re interested in: beautifully crafted spaces of historical and architectural significance that we can refine and evolve.
“Our Shakespeare Tower project is another good example of that. We were approached by a filmmaker and an artist who were downsizing and moving to the 28th floor of the tower. Modern Works worked closely with the couple to design and deliver a series of bold but careful choices to update and develop the interiors, which were reconfigured to enhance the flow of light. The galley kitchen was updated with a new stainless-steel counter, integrated lighting and modern appliances, while a new colour palette – matched from a dark-blue handle on the original fire escape door – echoes the original spirit of the building.
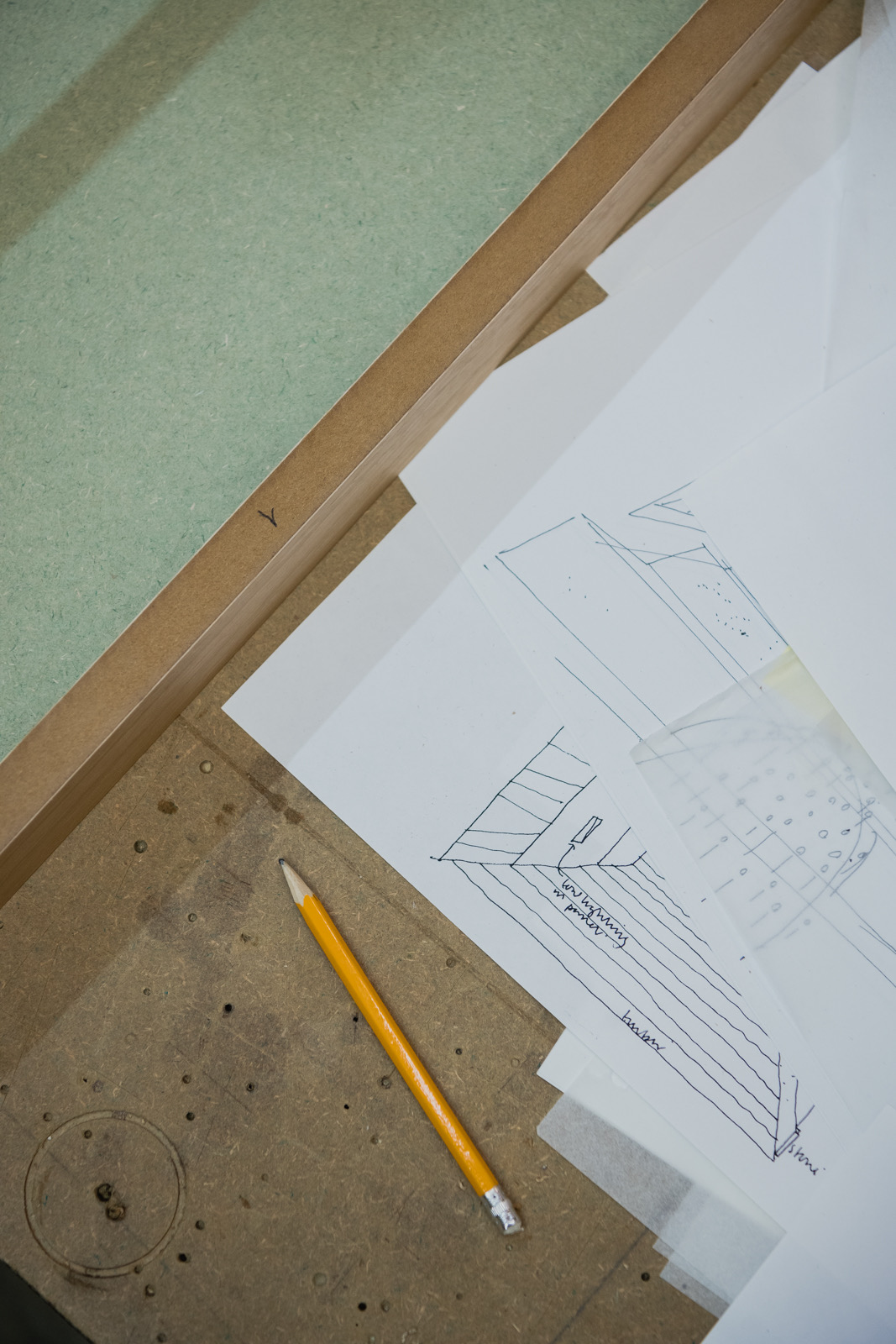
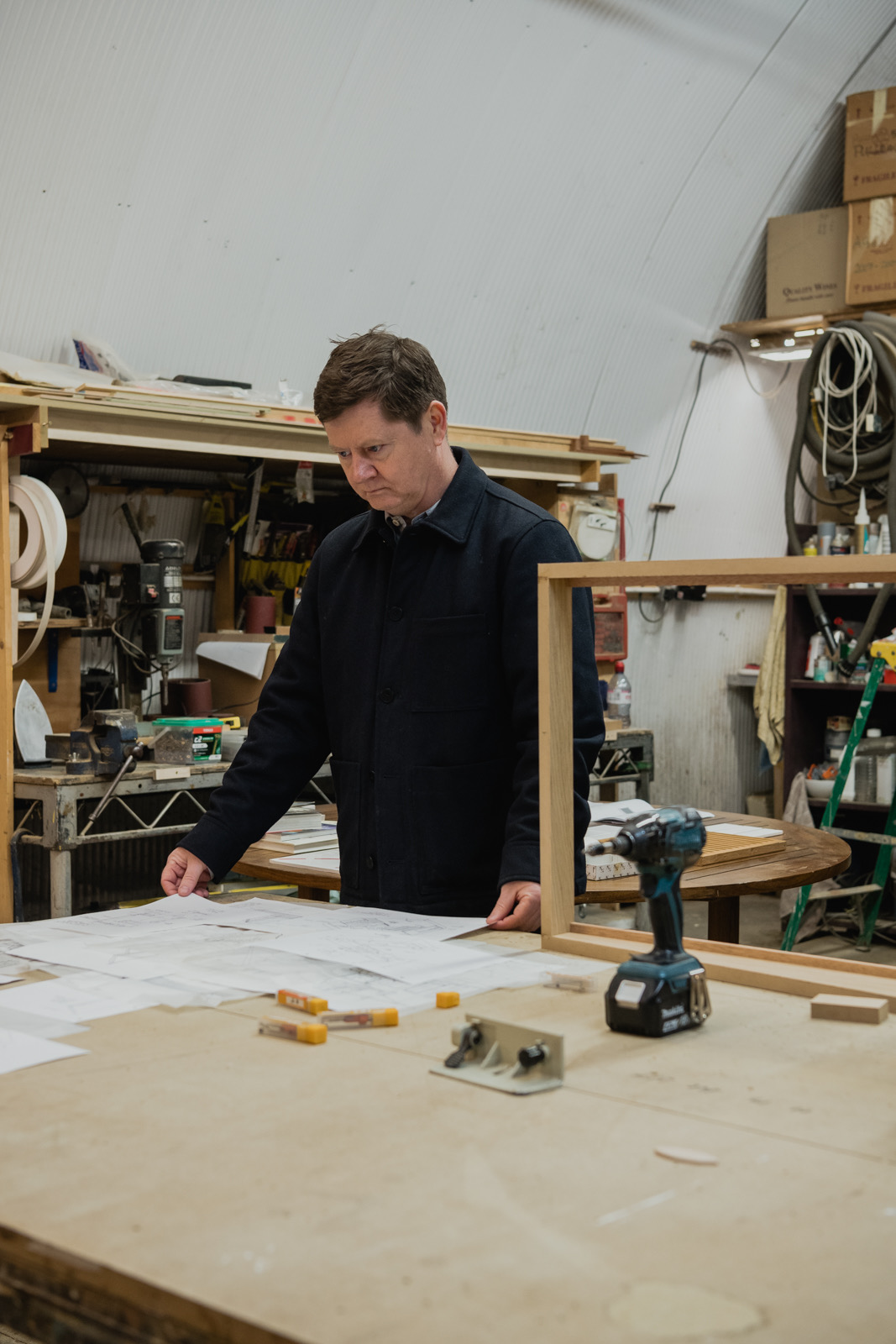
“We’re currently finishing off a project in Bloomsbury at the moment. The building has a very reduced aesthetic and Modern Works has designed a beautiful, Donald Judd-like kitchen for the clients, made from solid cherry wood. Had we not had the ability to explore this material in our own workshop, we would never in a million years have specified this material.
“The workshop has become an exciting place for both designers and architects: it reminds the team what our work is really all about. In many ways, it’s become an extension of our creative processes. It gives us the freedom to experiment – to make prototypes and to try new things. That freedom has enabled us to refine our processes and land on a certain way of doing things. We’ve developed a set of methods and components that we use for each project – whether that’s the ironmongery or the way in which we design a drawer. Each decision is the result of extensive research – and through that research, Modern Works has generated its own design language, which sits alongside Quinn Architects’ portfolio of large-scale projects.
“We don’t want to reinvent the wheel for each project – that’s not what we’re about. If we discover a better way of doing things, we’ll still use standardised parts – we’re not wedded to making everything ourselves. In that way, I see Modern Works as more of a cultural endeavour, intent on designing, researching and delivering work that we think is made in the best possible way.”